Магнитогорские птицеводы сэкономят более 3 млн рублей в год благодаря технологиям бережливого производства
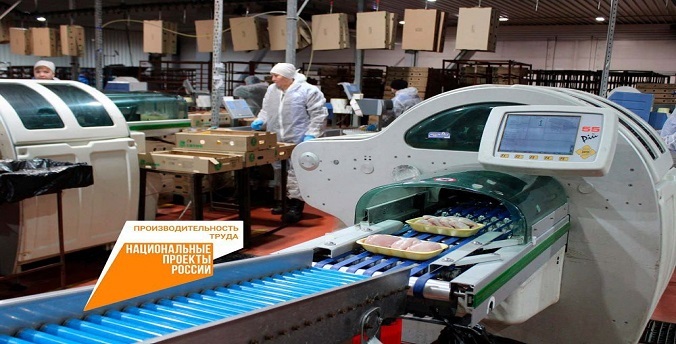
Магнитогорский птицеводческий комплекс, выпускающий продукцию под брендом «СИТНО», стал участником нацпроекта «Производительность труда»
Ожидаемый экономический эффект от проведенных за полгода участия в национальном проекте «Производительность труда» мероприятий на Магнитогорском птицеводческом комплексе (МПК, выпускает продукцию под брендом «СИТНО») составит 3,3 млн рублей в год. Это результат внедрения инструментов бережливого производства, на 45% ускоривших выпуск варено-копченой грудки на пилотном участке. Добиться успеха крупнейшему на Южном Урале производителю мяса птицы помог эксперт Регионального центра компетенций (РЦК, создан на базе Фонда развития промышленности Челябинской области) Руслан Салимов.
Под его руководством собранная из сотрудников предприятия рабочая группа проанализировала поток-образец, выявив на нём 66 проблем. Устранить их позволили технологии бережливого производства.
«Проведённые в рамках нацпроекта мероприятия помогли нам ускорить выпуск одного из самых востребованных продуктов из мяса птицы – варено-копченой грудки. Выработка по этой позиции за полгода увеличилась почти в 1,5 раза. Такой результат впечатлил не только руководителей нашего комплекса, но и всех сотрудников. Так, смена у тех, кто трудится на пилотном потоке, сократилась на 14%, но за это время сотрудник успевает сделать на 10% больше, чем раньше. Опытный эксперт РЦК помог нам не только максимально эффективно выстроить работу на потоке, расшить узкие места, но и обучил людей, показал конкретную, практическую пользу инструментов бережливого производства в действии. Теперь наша рабочая группа готова оптимизировать остальные производственные потоки МПК», – делится директор по качеству и производственным системам ООО «МПК» Егор Тимофеев.
Производственный анализ выявил участки, тормозившие весь рабочий процесс. Так, например, на этапе засолки специалист, кроме своей непосредственной задачи, занимался также доставкой со склада сырья, взвешивал его, убирал грязные ящики. Эти вспомогательные функции передали грузчику, чтобы мастер-засольщик не отвлекался. На участке термообработки наладили поставку сырья строго по графику. Это исключило «нахлесты» партий друг на друга, в разы сократив запасы сырья на складе, а показатель незавершенного производства в итоге уменьшился на 10%. Исключили и лишнее перекладывание продукции из тары в тару. Проанализировав передвижения сотрудников по цеху на участке «фасовки и упаковки», рабочая группа пришла к выводу, что необходимо перегруппировать рабочие места так, чтобы упаковщики готовой продукции не мешали друг другу. Эти и другие решения в комплексе позволили оптимально выстроить поток, увеличив выработку с 20,3 до 24,2 килограмм на человека в час, а общий показатель выпуска варено-копченой грудки улучшив на 45%.
Кроме того, предприятие сократило потери на упаковочном материале. Раньше из-за большого, не по продукции, размера пакета оставались длинные «хвосты». Выбрав на участке фасовки упаковку меньшего размера, предприятие всего за два месяца сэкономило сотни тысяч рублей.
«Изначально в нацпроекте не было предприятий из «пищёвки», и многие до сих пор уверены, что мы помогаем в основном обрабатывающей промышленности. Между тем, из более чем 120 южноуральских компаний, присоединившихся к нацпроекту на данный момент, около 20 – из пищевой индустрии. Представители этой сферы проявляют к философии бережливого производства всё больший интерес. И это понятно, ведь специфика отрасли диктует необходимость отладить производственную систему так, чтобы нигде не было простоев и задержек, мешающих соблюсти сроки годности и другие важные моменты. Конечно, работая на таких предприятиях, нашим экспертам приходится адаптировать привычные инструменты и методы под санитарные нормы и другие особенности деятельности пищевиков. Но они справляются, что доказывают результаты, полученные в ходе нацпроекта на «Ниагаре», «Мясном регионе», «Чепфе», а теперь и на МПК», – говорит директор Фонда развития промышленности Челябинской области Сергей Казаков.
После завершения активной фазы нацпроекта, когда эксперт РЦК присутствует на производственной площадке практически ежедневно, коллектив Магнитогорского птицеводческого комплекса самостоятельно продолжит внедрять инструменты бережливого производства на остальных потоках. Новые знания и навыки, приобретенные в нацпроекте «Производительность труда», будут применены на всех участках – от выращивания птицы до выпуска продукции глубокой переработки. В итоге за три года работы в нацпроекте предприятие оптимизирует производство всего птицеводческого комплекса целиком.
Фото: ООО «МПК»