Вагончик тронется
Развеиваем мифы об участии компаний в нацпроекте «Производительность труда»
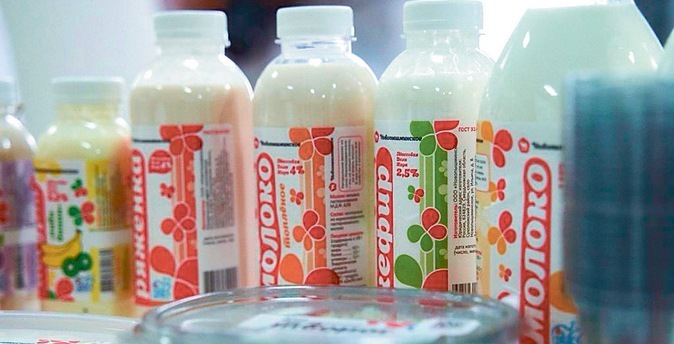
Эксперты РЦК помогли «Новопышминскому» найти 13 трудностей, которые «съедали» 805 минут рабочего времени.
У свердловских компаний остался последний шанс включиться в нацпроект «Производительность труда» в 2024 году
Пять лет назад Свердловская область стала одним из пилотных регионов, которые первыми включились в нацпроект «Производительность труда». За это время к программе присоединились 242 местные компании — от небольших предприятий до градообразующих холдингов разных отраслей: промышленности, сельского хозяйства, строительства, транспорта, торговли и других. У тех, кто хочет попасть в это число в 2024 году, остался последний шанс.
За пять лет нацпроект и используемые в нем инструменты бережливого производства доказали эффективность. Выработка оптимизированных участков выросла в среднем в полтора раза, время изготовления продукции сократилось на 40%, а запасы незавершенного производства — на 42%. Экономический эффект превысил три миллиарда рублей.
По данным опроса Регионального центра компетенций в сфере производительности труда Свердловской области (РЦК), местного оператора госпрограммы, 92% компаний удовлетворены участием в нацпроекте: их ожидания оправдались. Об этом же говорят областные власти.
— Я общался с руководителями разных предприятий: малых и крупных компаний, вчерашних стартапов и заводов, которым не один десяток лет. Ни один собственник не пожалел, что включился в национальный проект, каждый увидел конкретные результаты, — рассказывает Алексей Шмыков, первый заместитель губернатора Свердловской области и куратор нацпроекта «Производительность труда» в регионе.
Доказательством эффективности государственной программы и методик РЦК стало и участие в нацпроекте крупного бизнеса.
- Такие компании вначале осторожничали, присматривались. Только в 2021-22 годах, когда накопилась «критическая масса» положительных примеров и они убедились в результативности методик РЦК по внедрению инструментов бережливого производства, в госпрограмму вошли крупные холдинги - «Уралэлектромедь», «ВСМПО-Ависма», Каменск-Уральский металлургический , Синарский трубный заводы и другие, - вспоминает Александр Казаков, генеральный директор областного Фонда технологического развития промышленности Свердловской области, на базе которого функционирует местный РЦК.
Но даже спустя пять лет среди потенциальных участников нацпроекта живы мифы о бережливом производстве и эффективности его инструментов. Вот четыре самых популярных возражения и четыре компании, которые верили в них.
«У РЦК нет опыта в нашей сфере. Чем он сможет помочь?»
• Предприятие — «Урал-Логистик» • Время работы на рынке — 27 лет • Сфера — розничная торговля косметикой, парфюмерией и бытовой химией • Пилотный проект — товародвижение заказа с распределительного центра в магазины, управление товарно-материальными ценностями на распределительном центре • Доля «пилота» в выручке предприятия – 90% • Результаты: На 28% выросла выработка На 100% снизилось НЗП На 33% сократилось время приемки и размещения товара |
Компания «Урал-Логистик» поставляет косметику, парфюмерию и бытовую химию через собственные сети Lamel и Оптима. Ей принадлежат 106 магазинов, распределительный центр и два кросс-дока. В рамках госпрограммы компания оптимизировала управление товарно-материальными ценностями на распределительном центре.
— Мы несколько месяцев сомневались, подходит ли нам нацпроект, стоит ли участвовать в нем. Думали, методы бережливого производства более эффективны в промышленных компаниях, и не понимали, будут ли они полезны для нас, —признается Анастасия Торощина, руководитель департамента логистики компании. — Оказалось, lean-инструменты эффективны не только в промышленности.
С помощью экспертов РЦК в «Урал-Логистик» нашли узкое место — зону приемки распределительного центра. Рабочая группа разработала топологию склада, изменила расположение товаров и ячеек, дополнительно «расшила» участок по кросс-докинговым ячейкам. В результате этих и других мер доля незавершенного производства МТО снизилась до нуля.
— Особенность работы РЦК в том, что его специалисты не навязывают свое мнение и методики — они подсвечивают узкие места и на практике, решая выявленную проблематику, передают инструментарий, с помощью которого сотрудники смогут самостоятельно решать проблемы производственных цепочек в дальнейшем. Как использовать эти инструменты и развивать производственную систему, решает само предприятие, — рассказывает Александр Казаков, генеральный директор областного Фонда технологического развития промышленности Свердловской области.
«Бережливое производство работает только в условиях конвейера»
• Предприятие — «Новопышминское» • Время работы на рынке — более 90 лет • Сфера — производство молочных продуктов • Пилотный проект — фасовка кефира • Доля «пилота» в выручке предприятия — 10% • Результаты: На 24% выросла выработка На 22% снизилось время выпуска продукции На 10% сократилась доля НЗП |
Многопрофильное агропредприятие полного цикла «Новопышминское» — один их лидеров сельского хозяйства Свердловской области по надоям молока. Включившись в нацпроект, компания оптимизировала выпуск кефира. Эксперты РЦК помогли найти 13 трудностей, которые «съедали» 805 минут рабочего времени — от нехватки ящиков до аварийных остановок. Главной проблемой оказалась ограниченная пропускная способность конвейера, из-за чего приходилось регулярно останавливать фасовку.
Чтобы увеличить пропускную способность, на предприятии приняли решение оборудовать закрывающийся проход между цехами и изменить схему перемещений грузчиков, в три раза сократив их маршрут. До этого грузчики проходили по четыре километра за смену и тратили на перемещения между участками 90 минут.
— Мы долго сомневались, вступать ли нам в нацпроект. Думали, программа больше подходит предприятиям конвейерного типа, таким как металлообработка. Но сомнения развеялись уже на мастер-классе РЦК, где своим опытом делились другие компании. После этого мы сами убедились — бережливое производство работает с любыми процессами, — вспоминает генеральный директор предприятия Любовь Вяткина.
— Одно из главных достоинств и преимуществ бережливого производства — в его универсальности. Оно основывается на оптимизации повторяющихся процессов, из которых состоит любая деятельность. Потому lean-методики работают везде: от АПК и промышленных холдингов до логистических компаний, — объясняет Александр Казаков.
«Lean-инструменты решат проблемы раз и навсегда»
• Предприятие — «ИнвестПроект» • Время работы на рынке — 13 лет • Сфера — горнопромышленная • Пилотный проект — изготовление щебня еврофракции 4 — 8 • Доля «пилота» в выручке — 14% • Результаты: Время работы сократилось на 24% Выработка выросла на 31% НЗП сократилось на 21% |
Компания «ИнвестПроект» добывает и продает щебень для строительства автодорог. Пилотным проектом руководство выбрало один из самых трудоемких процессов — изготовление щебня еврофракции размером 4 — 8 мм.
Приглашенные эксперты РЦК помогли найти в работе потока более 100 проблем. Главной оказалась низкая производительность участка отгрузки железнодорожным транспортом. Чтобы поднять его эффективность, на предприятии внедрили почасовой производственный анализ и систему 5С. Установив вдоль железнодорожных путей дополнительные стеллажи с тормозными башмаками, время закрепления группы из 49 вагонов сократили на 70% - со 116 до 34 минут. Отремонтировав гидромолот, избавились от зависаний горной массы в камере дробления, которые в общей сложности «съедали» 21,2 часа рабочего времени.
— Во время реализации проекта на первом месте стояли текущее производство и борьба с постоянно возникающими проблемами. Мы относились к проекту по остаточному принципу, так как нужно было здесь и сейчас выполнить план, — рассказывает генеральный директор компании Сергей Филимонов. — Но пришло понимание, что над созданием бережливого производства нужно работать постоянно: собирать данные и анализировать их, выявлять коренные причины трудностей. Если этого не делать, проблемы будут накапливаться как снежный ком, а силы и ресурсы —тратиться впустую.
В компании «ИнвестПроект» отремонтировали гидромолот и избавились от зависаний горной массы в камере дробления, которые в общей сложности «съедали» 21,2 часа рабочего времени.
— У РЦК нет волшебной палочки, которая раз и навсегда решит трудности компании. Наша задача — передать команде методологию работы, научить сотрудников находить потери, неэффективности и выявлять из них коренные, помочь сделать борьбу с ними системной, чтобы она не превращалась в ежедневное тушение пожара. Только тогда получится разработать решения, которые исключат появление проблем в будущем, — уверена руководитель проектов свердловского РЦК Александра Пученкина.
«Фабрика процессов — бесполезное обучение»
• Предприятие — Артемовский машиностроительный завод «Вентпром» • Время работы на рынке — более 80 лет • Сфера — производство и модернизация вентиляционной продукции для шахт, метрополитенов, транспортных тоннелей, промышленных предприятий • Пилотный проект — изготовление роторов ВОМ 24 • Доля «пилота» в выручке предприятия — 11% • Результаты: На 28% выросла выработка На 77% уменьшилось время выпуска продукции На 33% уменьшился объем незавершенного производства |
В качестве пилотного проекта руководство выбрало изготовление роторов ВОМ 24 для вентиляции тоннелей и станций метрополитенов. Эта продукция пользуется постоянным спросом, но сроки ее изготовления сильно колебались.
«Вентпром» параллельно выпускает десятки уникальных, технически сложных изделий из сотен элементов. Из-за этого трудно было выстроить процесс так, чтобы детали - собственного производства и приобретенные - приходили на сборочные участки точно в срок, в том комплекте и порядке, в котором они собираются. С помощью экспертов РЦК и рацпредложений сотрудников на пилотном потоке упорядочили и заметно сократили производственный цикл, освободили существенную долю производственных и интеллектуальных ресурсов. В этом помогло обучение на «Фабрике процессов» свердловского РЦК.
— Отношение к тренингу у меня было предвзятым. Изделия «Фабрики…» совсем не похожи на наши. Я не мог понять, как навык сборки регулятора давления газа поможет нам в работе. Но он помог: на простых примерах мы научились видеть потери и неэффективности, получили практический опыт применения инструментов бережливого производства. Это позволило по-новому взглянуть на процессы своего предприятия, — вспоминает Владимир Яллин, инженер-технолог «Вентпрома».
— Такой тренинг дал толчок в работе и сплотил команду. Мы стали лучше и быстрее договариваться друг с другом. Кроме того, «Фабрика» помогла победить сопротивление некоторых сотрудников и скепсис по отношению к методам бережливого производства, — согласна с коллегой инженер-технолог предприятия Галина Кораблева.
«Вентпром» — градообразующее предприятие Артемовска и единственный в России производитель вентиляторов главного проветривания для шахт, тоннелей и метрополитенов.
Фабрика процессов РЦК
«Фабрики процессов» — это центры обучения РЦК, где воссоздан типичный офисный и производственный процесс. В их работу сознательно включили потери и неэффективности, которые участники под руководством тренеров учатся оптимизировать: логистику и ресурсы, сокращать производственные площади, балансировать загрузку операторов, выстраивать работу подразделений в одном ритме.
Каждый тренинг длится восемь часов и состоит из серии лекций, деловых игр и практических сессий с использованием инструментов бережливого производства. Полученные навыки участники затем применяют в своей компании: устраняют потери, снижают издержки, повышают производительность труда.
- Я была на нескольких «Фабриках», и с тех пор советую пройти такие тренинги всем. Благодаря небольшому размеру и простоте «цеха» или «офиса» в них быстро становятся видны все недочеты. Проще понять, как упростить работу, сделать ее быстрее, эффективнее – и как использовать эти навыки в своей компании, - делится опытом Татьяна Щеглова, соучредитель «Гросс Групп ЕК».
Каждый тренинг длится восемь часов и состоит из серии лекций, деловых игр и практических сессий с использованием инструментов бережливого производства. Полученные навыки участники затем применяют в своей компании: устраняют потери, снижают издержки, повышают производительность труда.
Обучение на «Фабриках процессов» Свердловского РЦК прошли более двух тысяч человек. Для предприятий — участников нацпроекта такие тренинги бесплатны. На коммерческой основе в них может участвовать любая компания.
Алексей Шмыков, первый заместитель губернатора Свердловской области:«За пять лет нацпроект «Производительность труда» доказал свою эффективность. Вместе с другими госпрограммами он помог решить стратегические задачи, которые встали перед страной: преодоление импортной зависимости, расширение номенклатуры продукции, применение новых технологий, обеспечении экономической безопасности. Предприятиям-участникам нацпроект дал лучшие наработки в сфере бережливого производства и развития производственной системы, причем бесплатно. Он стал уникальной возможностью, которую компаниям нужно использовать. Времени осталось немного: участие в нацпроекте занимает полгода, перед этим нужно подготовить и согласовать заявку. Поэтому тем, кто хочет участвовать в программе и успеть «запрыгнуть в последний вагон», стоит поторопиться». |
Фотографии предоставлены пресс-службой РЦК