Дьявол в мелочах
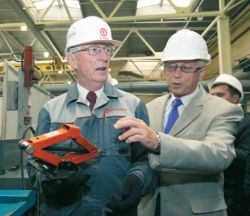
Повышение производительности труда провозглашается первыми лицами нашей страны в качестве одной из приоритетных задач на ближайшие годы. Без ее достижения всерьез говорить о России как о конкурентоспособной мировой державе будет невозможно. Однако пока, по свидетельствам экспертов, лишь небольшая часть отечественных предприятий всерьез озабочена этим вопросом.
«Пока компания работает более или менее успешно, никто из менеджеров не хочет думать о деталях, о том, что можно работать чуть лучше здесь и чуть лучше там, - констатирует международный эксперт в области технологий бережливого производства Майкл Вейдер. - Детали становятся важны, только когда начинаются проблемы, на которые менеджмент уже не может закрывать глаза. Но насколько успешнее работает предприятие, если технологии бережливого производства его руководство начинает использовать еще до того, как грянул гром!». Что из себя представляют эти технологии и чему топ-менеджеры должны поучиться у домохозяек, объясняет Майкл Вейдер.
Без излишков
- Когда в теории управления появляются концепции бережливого производства? С чем связано попадание этой темы в фокус внимания специалистов по менеджменту?
- Отвечая на этот вопрос, можно прочитать двухчасовую лекцию. Однако если остановиться на отдельных ключевых моментах, то надо сказать, что идеи бережливого производства возникли еще в начале прошлого века в США.
Еще до Первой мировой войны Чарльз Аллен разработал методологию обучения сотрудников кораблестроительных предприятий, позволяющую в сжатые сроки добиться высокой производительности труда. Дело в том, что Корпорация флота военного времени Комитета США по судоходству выпустила директиву о десятикратном увеличении численности работников судостроительной отрасли. Предприятия вынуждены были набирать огромное количество неопытных людей, и разработки Аллена стали адекватным решением сложившейся проблемы. Свою систему обучения сотрудников он изложил в книге, вышедшей еще в 1919 году.
Позднее пытался найти и внедрить на своих заводах механизмы управления, способные минимизировать сопутствующие конвейерному производству потери, крупнейший американский промышленник Генри Форд. Тем не менее его идеи тогда не получили широкого распространения, поскольку значительно опережали время.
В начале Второй мировой войны на основе идей Аллена была создана концепция под названием Training within industry (TWI) - «Система обучения на производстве». Когда стало очевидно, что война окажется затяжной и в нее будет вовлечено все мировое сообщество, а значит, во всех областях индустрии значительно вырастет объем производства, американское правительство предприняло шаги для удовлетворения потребности в военной продукции. Служба TWI была сформирована в 1940 году, и программы, разработанные Ченнингом Райсом Дули, вводились в индустрию огромным количеством инструкторов-добровольцев, сеть которых работала по всей стране. Удивительно, но после войны многие принципы TWI были забыты большинством предприятий.
- Но технологии бережливого производства ассоциируются с японскими традициями менеджмента...
- Действительно, принципы TWI в дальнейшем стали популярны в Японии. Страна восходящего солнца, обладающая минимальными природными и человеческими ресурсами, да еще и серьезно пострадавшая в ходе военных действий, нуждалась в быстром возрождении промышленной инфраструктуры и консолидации населения. Именно поэтому владельцы японских предприятий обратились к опыту США, где уже использовались некоторые механизмы бережливого производства. В результате японцы существенно превзошли американцев, да и весь остальной мир, по производительности труда. И когда в 1980-е годы теоретики занялись исследованиями «японского чуда», в качестве основного фактора успеха они приводили идеи бережливого производства. Именно поэтому многие стали ошибочно полагать, что эта концепция - детище японцев.Сегодня в мировом словаре бережливое производство обозначается терминами «лин-технологии» (от английского lean - «без излишков») и «кайдзен» (kaidzen), введенными Массаки Имаи в 1986 году для описания принципов менеджмента японских компаний. И хотя эти названия стали общеупотребимыми всего 25 лет назад, я постарался показать, что идеи, стоящие за ними, имеют довольно долгую историю.
Пророк в своем отечестве
- Когда эти идеи пришли в Россию?
- В начале ХХ века у вас был собственный специалист, излагавший идеи бережливого производства, очень близкие к тому, о чем говорили американцы. Его имя - Алексей Гастев. Он изложил свои взгляды на организацию производственного процесса еще в 1924 году в книге «Трудовые установки», а позднее стал автором еще ряда работ по научной организации труда. Примечательно, что Гастев состоял в переписке с Генри Фордом, так что его идеи находились в общемировом тренде. Печально, что в 1938 году Гастев был арестован НКВД, а потом расстрелян. Стоит ли говорить, что его работы в Советском Союзе были на долгие годы забыты?
Собственно, возвращение принципов бережливого производства в Россию уже под видом современных лин-технологий произошло только в начале 2000-х годов. Приехав сюда впервые в 2003-м как консультант, я столкнулся с тем, что эти технологии используются только на отдельных предприятиях, да и то локально. Однако потребность в их внедрении уже назрела: с одной стороны, в Россию стали приходить и строить предприятия зарубежные инвесторы, с другой - сами российские компании начали выходить на международные рынки и осознавать, что для успешной конкуренции в глобальном масштабе нужны другие принципы менеджмента и организации производства.
Губительное незнание
- Вы говорите о разных компаниях из разных отраслей, но неужели технологии бережливого производства универсальны и не зависят от масштаба и специфики бизнеса?
- Технологии бережливого производства успешно применяются в самых разных организациях: и на заводах, и в банках, и в транспортных компаниях, и в ресторанах, и в салонах красоты - практически везде. Дело в том, что на самом деле все бизнесы, по сути, одинаковы и сталкиваются с одними и теми же проблемами.
Самая главная проблема в том, что бизнес-процессы не сконцентрированы на работнике. Менеджер или инженер разрабатывает некий процесс, потом создает техническое задание для подчиненных и спускает его вниз. Но менеджер или инженер не работает своими руками, он конструирует процесс, исходя из своих представлений о том, как он протекает и каким должен быть. Но нельзя, условно говоря, указывать человеку, как ему лучше работать молотком, если ты сам никогда этот молоток в руках не держал. А между тем это повсеместная ситуация: управленцы считают, что знают технологический процесс, а на самом деле они имеют о нем очень приблизительное представление и при этом ни за что не хотят в этом признаваться.
- То есть проблема в том, что руководители банально не знают, как на самом деле работают их компании?
- Руководители в какой-то момент просто перестают обращать внимание на то, что происходит на уровне рядовых сотрудников, на то, как они работают. В концепции бережливого производства есть такой термин «гэмба». Он обозначает рабочее место рядового сотрудника. Понятно, что если речь идет о промышленном предприятии, то это может быть конвейер или цех, если о ресторане - кухня, если о банке - зал, где сидят операционисты. И так далее.
Так вот, когда я общаюсь с руководителями компаний, то начинаю беседу с вопроса, как давно они посещали «гэмбу». Большинство начинают смущаться, потому что не бывали там многие годы. Потом спрашиваю, что конкретно делает рядовой сотрудник компании на своем рабочем месте - буквально прошу расписать этот процесс по шагам. Практически ни один руководитель не может дать ответ на этот, казалось бы, простой вопрос. Тут-то и становится очевидно, что между руководителями и подчиненными огромная пропасть, но чем ближе к производству находится менеджер, тем больше времени он должен уделять посещению «гэмбы».
Детальный разбор
- Хорошо, так менеджеры будут лучше знать бизнес-процессы в своей организации. И как это поможет им сделать производство бережливым?
- Бережливое производство - это производство, где ликвидированы или сведены к минимуму различные потери и издержки при изготовлении продукции, ее обработке, транспортировке, реализации. Брак и перепроизводство - это тоже виды потерь. Но чтобы избежать всех этих потерь, надо знать, где и из-за чего они возникают. А как это узнать? Управляя компанией, невозможно их увидеть: в глаза бросается только что-то совсем вопиющее, а остальные издержки «прячутся» - немного здесь, немного там. Чтобы разглядеть их, руководителям и нужно досконально знать, как работают их сотрудники и где возникают проблемные зоны.
- И что нужно делать дальше, чтобы устранить выявленные потери?
- Главное - обучение всех работников технологиям бережливого производства. Они очень просты и фактически основываются на элементарном здравом смысле. И начинаются они с усвоения сотрудниками тезиса о том, что на их рабочем месте все должно быть устроено так же логично, комфортно и аккуратно, как, например, у домохозяйки на кухне. Все должно быть чисто, под рукой и возвращаться на свое место после проведения той или иной операции. В этом нет ничего сложного, а между тем скорость выполнения той или иной операции может зависеть от того, например, с какой стороны у человека находятся рабочие инструменты. Если внимательно наблюдать за сотрудниками, научить их следить за собственными действиями, можно заметить много интересных деталей, влияющих на производительность труда. А из этих деталей складывается работа компании в целом.
Видимая рука государства
- Как можно стимулировать предприятия внедрять технологии бережливого производства?
- Здесь есть два способа. Первый - просветительская работа. Как я уже говорил, за те десять лет, что я приезжаю в Россию и веду здесь обучение технологиям бережливого производства, прогресс очевиден. Люди смотрят на коллег, которые стали добиваться большего, применяя лин-технологии, и хотят сами им научиться. Другие бизнес-тренеры также рассказывают на своих тренингах о лин-менеджменте, доносят его идеи до широкой общественности через СМИ. Постепенно это дает свои результаты.
Есть и второй путь - государственное стимулирование предприятий, использующих эти технологии. В ряде стран власть, например, частично финансирует обучение основам лин-менеджмента, если организация выражает готовность освоить этот инструментарий (причем даже если это частная, а не государственная компания). В России, на мой взгляд, это было бы хорошим стимулом для предпринимателей.
Но ни первый, ни второй путь не приведут к успеху без заинтересованности самих руководителей компаний. Поэтому нам остается уповать на их сознательность и способность видеть перспективу.