Революция машин
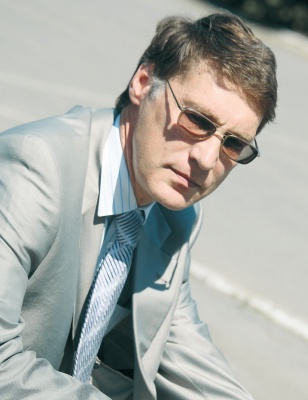
10 июля в Нижнем Тагиле открывается совместное российско-японское предприятие «Мишима-Машпром» по разработке, производству и восстановлению комплектующих для машин непрерывного литья заготовок стали — кристаллизаторов. На паритетных началах СП владеют инжиниринговое ЗАО НПП «Машпром» (Екатеринбург) и японская Mishima Kosan (крупнейший разработчик и производитель кристаллизаторов в Японии). Общий объем инвестиций в проект — около 7,5 млн евро. Партнеры собираются выпускать кристаллизаторы с высоким ресурсом эксплуатации. Японская сторона вкладывается уникальными технологиями производства, российская — оборудованием и собственными наработками в области повышения износостойкости деталей. Для уральской инжиниринговой компании такое сотрудничество — возможность укрепить бизнес на фоне растущей конкуренции со стороны Китая. В условиях глобальной неопределенности на рынках металлургии Машпром уходит в нишу разработки и производства новых уникальных продуктов, которые могут быть востребованы вне зависимости от глобальной мировой конъюнктуры. О том, как инжиниринговая компания борется за место на машиностроительном рынке, рассказывает управляющий директор Машпрома Александр Котельников.
Спекание технологий
— Почему в партнеры вы пригласили именно японскую компанию?— Проблемой повышения ресурса кристаллизаторов МНЛЗ мы занимаемся уже семь лет в сотрудничестве с кафедрой сварки УГТУ-УПИ (работу со стороны университета возглавляет профессор Юрий Коробов). Знакомство с компанией Mishima Kosan для нас было крайне важно — она основной в мире разработчик технологий в этой области. Но началось оно осторожно. Были опасения, что применение японских технологий в российских реалиях не даст ожидаемого эффекта. Поэтому после долгих переговоров по японской технологии были разработаны и изготовлены два комплекта кристаллизаторов, которые для тестовых испытаний мы установили на МНЛЗ № 4 Нижнетагильского металлургического комбината. Все, от управляющего директора комбината до рабочих на разливке стали, поддержали проект.
В результате к июлю 2012 года на этой МНЛЗ был установлен мировой рекорд стойкости слябовых кристаллизаторов — они выдержали разливку более 600 тыс. тонн стали. Это в восемь раз больше, чем у лучших западных образцов. Такого эффекта не ожидал никто. Страх ушел, и у нас появилась уверенность в необходимости внедрения японских технологий в России. Мы предложили Mishima Kosan создать СП и локализовать производство таких кристаллизаторов.
— Можно было просто купить лицензию.
— Японская сторона на этом и настаивала. Но для нас это не интересно: наука и техника стремительно развиваются, и если мы купим лицензию на кристаллизаторы, то уже через 3 — 5 лет начнем отставать от конкурентов (тех же японцев). Тогда нам придется покупать лицензии снова и снова.
К тому же нам было что добавить со своей стороны: несколько лет назад для решения проблем повышения ресурса службы различных изделий мы создали на нашей площадке в Нижнем Тагиле участок газотермического напыления, который хорошо себя зарекомендовал.
— При чем здесь напыление?
— Секрет стойкости кристаллизаторов МНЛЗ в их покрытии. Если его не использовать, оборудование выдержит не более
50 плавок (7,5 тыс. тонн разливки стали). Сегодня делают покрытия из медных сплавов, гальванопокрытия с применением никеля и кобальта, что уже позволяет выдерживать 100 — 150 плавок. К этому добавили термообработку и увеличили износостойкость до 500 плавок. В Японии для достижения высоких результатов в совокупности с гальваническим применяют газотермический метод напыления. Он предполагает, что с помощью плазменной струи на поверхности детали распыляются особо мелкие порошки. Скорость струи при таком процессе примерно 70 тыс. метров в секунду, в семь выше скорости звука. Это заставляет порошки буквально сплавляться с поверхностью. Газотермический способ позволяет наносить порошки, имеющие в составе металлы и сплавы, которые невозможно перенести электролизом из-за их особой твердости. Состав очень сложен. За счет этого достигаются и высокая антикоррозионность, и износостойкость изделий.
— В чем новации вашего проекта?
— Мы считаем, что будущее за газотермическим напылением. Поэтому сделали японским партнерам смелое предложение — использовать при производстве кристаллизаторов только его, без гальваники. Плиты стенок таких кристаллизаторов можно восстанавливать от трех до пяти раз: изношенный слой снимается, делается новое покрытие и кристаллизатор возвращается в производство. Планируется, что таким образом парк кристаллизаторов в России может сократиться в два-четыре раза. Для понимания: один комплект кристаллизаторов стоит до 100 тыс. евро. Вот реальная экономия для комбинатов.
— Для ваших конкурентов это может стать большой проблемой.
— Прежде основными поставщиками кристаллизаторов в России были западные компании, главным образом европейские. Сегодня за нами пристально следят все крупнейшие игроки: КМЕ, Voestalpine, SMS. На старте проекта они убеждали потребителей, что заявляемых нами показателей достичь невозможно. А когда получилось, осознали, что зря расслабились, и стали предлагать российским металлургам свои новые разработки. Сейчас на рынке уже идет открытая конкурентная война на уровне технологий.
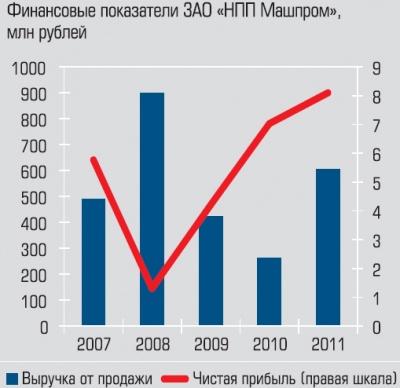
— Мы взяли на себя организацию производства кристаллизаторов, продвижение их на рынок, мониторинг состояния, сервис и последующее многократное восстановление. Оборудование закупили еще до создания СП, чтобы запустить предприятие в сжатые
сроки: от подписания соглашения о намерениях до выпуска первой продукции прошло всего полгода. Mishima будет проводить анализ работы существующих кристаллизаторов исходя из реальных условий эксплуатации и реинжиниринг. Это достаточно сложный процесс, требующий специального софта, мощнейших компьютеров и, самое главное, уникальных специалистов. В этом с японскими коллегами никто не может сравниться. Mishima также будет поставлять специально разработанные порошки для газотермического напыления, смешивая их в нужной пропорции, и предварительно обработанные стенки кристаллизаторов.
В России в рамках СП пойдет наиболее ответственная часть работ: напыление, термическая обработка, правка на мощных прессах с высокой точностью и последующая финишная обработка на современных точных станках. Сейчас в Японии проходят обучение наши инженеры: знания и умения в данном процессе имеют определяющее значение. От рабочих требуется уникальное «ощущение» металла.
— Каких показателей хотите достичь?
— В первый год планируем произвести 13 комплектов кристаллизаторов, через три года выйти на проектную мощность в 70 комплектов в год и занять до 70% рынка кристаллизаторов РФ. Затем пойдем на рынки СНГ и Европы.
Идите в инжиниринг
— Команда Машпрома вышла с Уралмашзавода. Соседство с гигантом помогало или мешало развитию бизнеса?— В свое время он был лучшей кузницей кадров для машиностроения: с точки зрения и технологии управления, и инженерных подходов. Когда после 1991 года новое руководство Уралмашзавода не смогло определиться со стратегией развития предприятия и стало ясно, что инженерных перспектив практически нет, мы собрались и приняли решение самостоятельно реализовывать себя в качестве организаторов производства и инженеров. Идея заключалась в том, чтобы заниматься только инжинирингом, никаких производств: все изготавливать по кооперации на маленьких и больших заводах, компилировать и поставлять готовую продукцию покупателю. При этом полностью отвечать за результат.
Чтобы не конкурировать с Уралмашзаводом, мы нацелились на трубопрокатные заводы. В СССР все было четко поделено: Уралмаш занимался только МНЛЗ, станами горячей прокатки, гидропрессами, буровыми установками и карьерными экскаваторами. На трубопрокатных производствах специализировался завод тяжелого машиностроения в Подмосковье. Он был далеко, а 70% трубного производства соcредоточено на Урале. Для нас — очень удачно. Мы определяли проблему трубного предприятия, предлагали ее решить, причем модернизацией — не запчасть поставить, а новый узел с новыми качествами, более производительный, с повышенным ресурсом. А когда Уралмашзавод начал терять позиции, к нашим клиентам добавился сегмент ведущих металлургических комбинатов, таких как ММК и Евраз. Причем не только в черной металлургии, но и в цветной: заводы Русала, Норильского ГМК. Сегодня один из крупнейших наших заказчиков — ВСМПО: реализуем крупные проекты реконструкции прокатного производства, стоит вопрос о модернизации прессового производства, стана 2000.
— Компанией владеют несколько бизнесменов, включая вас. Пустить в Машпром новых партнеров не планируете, например, чтобы привлечь средства на развитие?
— Пока нет. На данный момент наиболее удобная для нас форма — создание СП. Например, у совместного предприятия с Mishima достаточно большой по российским меркам уставный капитал — 35 млн рублей. Живыми деньгами, без оборудования. И это только на старте.
— Для развития кредитуетесь или используете собственные средства?
— По-разному. Когда был кризис, и мы стояли два года, был переизбыток собственных оборотных средств. Понятно, что на подъеме мы начали кредитоваться. Сейчас стараемся держать баланс.
— Зачем инжиниринговой компании производство? Ваш машзавод в Нижнем Тагиле уже несколько лет показывает убытки.
— Мы создали его еще в 2009 году. Как инжиниринговая компания, Машпром активно размещал заказы у многих крупных производителей: Уралмаша, Уралхиммаша, Буммаша. Но когда они начали сокращать объемы производства, ухудшилось качество продукции, дисциплина сроков, перестали развиваться технологии. Нужно было срочно что-то предпринять, чтобы не потерять клиентов. Поэтому мы купили разрушенную промплощадку бывшего завода ЖБИ. Два года восстанавливали, организовали производство комплектующих, что позволило нам частично размещать заказы. Но его специфика — индивидуальное производство. Оно очень рваное: то перегруз, то недогруз. Проблема недозагруженности сегодня — общая практически для 100% машпредприятий России. По итогам 2012 года рентабельность машиностроения в целом была около 1,5 — 3% (включая оборонку, где деньги не считают). И основные генераторы убытков — производители индивидуальной машпродукции. Точка безубыточности нашего НТМЗ — 5 млн рублей в месяц. Наша цель — сохранить собственное производство, развить и укрепить его. Для этого — вывести завод на серийные заказы, чтобы их доля в общем портфеле достигала хотя бы 50%. Тогда будут стабильные загрузка, коллектив, зарплата. И СП с Японией как раз на это нацелено.
На ножах с Поднебесной
— Странным кажется создание нового производства оборудования для металлургии именно сейчас. Статистика настойчиво демонстрирует стагнацию в выпуске металлопроката, доходы металлургических гигантов сокращаются, да и основные инвестпроекты в отрасли практически реализованы.— Ситуация действительно очень напряженная. Во-первых, рентабельность металлургического производства в 2012 году снизилась с 18 — 20% до 4 —5%. Для металлургов это тяжелый удар. Плюс сильное давление со стороны Китая, который активно наращивает выпуск стальной продукции. Все думали, что в 2013 году они немного притормозят, а они дали прирост в 12% за полгода. Влияние Поднебесной на мировую металлургическую отрасль будет только усиливаться. Китайцы наметили создание глобальной металлургической компании — мирового лидера на базе Baosteel, под который соберут все металлургические активы.
Опасность в другом. Чтобы построить такое количество металлургических заводов, Китаю нужен был опережающий рост развития машиностроения. Учитывая, что цикл реноваций в металлургии 20 лет, страна получила теперь значительный объем незагруженных машиностроительных мощностей и начинает серьезно демпинговать. Они имеют дешевый металлопрокат, дешевую рабочую силу, суперсовременное машиностроительное производство, которое не загружено и готово работать на любых ценовых условиях, лишь бы получать заказы. Конкурировать с ними ни Запад, ни Россия ни в машиностроении, ни в металлургии не могут. Ведущие иностранные компании Voest Alpine, SMS-Demag, Danieli, чей инжиниринг весьма недешев, давно перенесли производство в Китай, что позволяет им предлагать готовую продукцию по цене заготовки. Даже мы гидравлический пресс для СП купили в Китае. Посмотрите на ценообразование: в России металлопрокат стоит 25 — 30 рублей за кг, а в Китае пресс 630 усилием тонн — 64 рубля за кг, хотя такое сложное инженерное сооружение должно стоить около 12 долларов за кг. Как можно изготовить в России такой гидравлический пресс за аналогичные деньги? Это же цена забора!
Соревноваться с Китаем Россия совершенно не готова: в Поднебесной государство под строительство нового завода предоставляет бесплатно землю и кредит на 20 лет под 0% годовых, а прежнюю площадку выкупает, засчитывая сумму в счет погашения кредита.
В результате в Китае активно строятся самые современные заводы.
— И какой выход?
— То, что мы в свое время успели создать на старых мощностях в Нижнем Тагиле новый завод, позволяет нам сегодня размещать здесь СП с японскими партнерами и занимать нишу продукции, где мы будем вне конкуренции. У китайцев таких уникальных проектов нет. Поэтому мы и дальше намерены смещать бизнес в сторону организации на этой площадке уникальных производств, которые позволят нам за счет новых технологий держать чистое конкурентное преимущество и не пускать на рынок китайцев и западные компании. Считайте это нашей реакцией на мировой кризис.
— У Машпрома сегодня разноплановое производство: от выпуска комплексов для металлургии до автоматических парковок. А недавно стало известно, что вы хотите построить на территории «Титановой долины» завод оборудования для переработки ТБО. Не перебор ли с диверсификацией? Или это тоже ответ кризису?
— Нам бы пора, наверное, себе на горло наступить, но жутко интересно. Все эти бизнесы так или иначе завязаны на металлургию и очень интересны с точки зрения инженерных подходов. Но автопаркинги и заводы по переработке ТБО — это проекты социального значения. Они направлены на решение экологических проблем больших городов, и для их реализации много препятствий. Все вроде понимают, что нужно освобождать улицы от машин и создавать многоуровневые автоматические парковки, убирать из центра города мусоровозы и строить заводы по уничтожению отходов. Но заказчиками строительства подобных объектов должны быть власти — нигде в мире такие проекты не являются коммерческими. Нам потихоньку удается продвигать эти направления на уровне региональных властей. Есть уже примеры многоуровневых парковок в Санкт-Петербурге, на очереди проекты в Екатеринбурге, Тюмени, Москве. Недавно был подписан протокол о намерениях между правительством Свердловской области и Mitsubishi Heavy Industries, которая обладает наиболее совершенными технологиями переработки ТБО. Мы понимаем, что подобные направления требуют ломки менталитета и на скорый эффект не рассчитываем. Но рано или поздно они прорвутся. И мы хотим быть одними из первых, кто сможет предложить рынку и современную продукцию, и технологии.