Адаптация производства к условиям цифровой «зеленой» экономики
Российская промышленность переживает процесс всесторонней трансформации. Модернизация устаревших производственных мощностей и неэкологичных технологий, на базе которых до сих пор функционируют многие промышленные предприятия со времен Советского Союза, идет параллельно с проектами по цифровизации. В последние годы в промышленных отраслях разворачиваются крупнейшие стройки и инвестпроекты. Идет модернизация основных средств и инфраструктуры. Особенно этот процесс ощутим в горнодобывающем и металлургическом секторе, так как именно эти отрасли сегодня сосредоточены на максимальном повышении эффективности производства и снижении экологического следа.
О том, почему крупнейшие предприятия связывают комплексное строительство с реинжинирингом производственных процессов и их цифровизацией и кто может реализовать такие проекты «под ключ», рассказал заместитель генерального директора, директор по работе с предприятиями горно-металлургического комплекса ИT-компании КРОК Олег Терехов.
С 2000-х годов российские горнодобывающие и металлургические компании проводят интенсивную модернизацию производственных мощностей. Проекты направлены на повышение эффективности — увеличение объемов производства при одновременном снижении издержек. Фактически это основной драйвер для модернизации отрасли. Справедливости ради надо сказать, что уже 20 лет назад передовые технологические решения развивались в том числе с учетом снижения воздействия на окружающую среду, таким образом, достигая коммерческих результатов, производства становились более экологичными. Сегодня вопрос воздействия производств на экологию вышел на первый план, и стало очевидным, что для улучшения экологической ситуации недостаточно просто модернизировать производства, необходимо направлять усилия непосредственно на решение проблем окружающей среды. Одним из инструментов, способным существенно помочь предприятиям в экологизации производств, являются цифровые технологии, позволяющие значительно сократить сроки и стоимость внедрения решений, а в ряде случаев реализовать те задачи, которые еще 20 лет назад казались абсолютно фантастическими.
Технологии для соответствия новым экологическим нормам
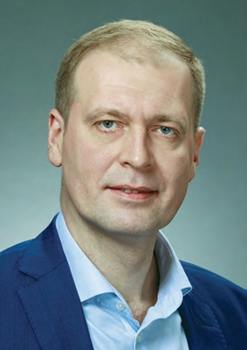
Как отмечает Олег Терехов, за последние годы серьезно ужесточились требования со стороны регуляторов к охране окружающей среды, вопросам устойчивого развития, повышению уровня охраны труда и промышленной безопасности в целом.
Еще в 2019 году Минприроды России утвердило новые экологические требования в отношении промышленных предприятий-«загрязнителей», запустив поэтапный переход на наилучшие научные технологии (НДТ) с целью эффективного предотвращения и контроля выбросов загрязняющих веществ в атмосферу, их сбросов в водные объекты и поступления в почву.
В текущем году Советом федерации РФ одобрен новый федеральный закон, призванный регулировать уровень выбросов парниковых газов. Кроме того, в скором времени нас ждет обновление климатического законодательства, в рамках которого Минэкономразвития разработало систему штрафов для крупнейших эмитентов выбросов парниковых газов за непредоставление или нарушение порядка подачи отчетности.
Следуя нормам законодательства, горнодобывающие и металлургические компании ведут учет выбросов парниковых газов и других вредных веществ в атмосферу, для чего внедряют в том числе цифровые решения на основе больших данных, облачных вычислений, IIоT, видеоаналитики и пр.
В качестве примера Олег Терехов приводит систему экомониторинга, которую ИТ-компания КРОК в настоящее время реализует на одном из металлургических предприятий. Эта система в режиме реального времени позволяет моделировать состояние атмосферного воздуха при фактических метеоусловиях и с учетом всех возможных источников выбросов и помогает определять основных вкладчиков в загрязнение атмосферы.
Набирает популярность технология цифровых двойников производственных объектов, в т.ч. технологических процессов. Цифровые двойники — математические модели — дают возможность выбирать оптимальные режимы работы, ставить виртуальные эксперименты, которые в реальности могут быть сопряжены с риском нанесения вреда сотрудникам предприятия, окружающей среде или оборудованию.
Инвестиционные программы предприятий сегодня формируются с учетом соответствия требованиям «зеленого» производства, а закладываемые технические решения соотносятся с принципами Индустрии 4.0, что позволяет применять самые современные цифровые решения на этапе модернизации или строительства производственных объектов.
«Только в 2021 году мы можем отметить целый ряд строек и проектов по модернизации, которые в связке с цифровизацией можно отнести к разряду «зеленых» и соответствующих целям устойчивого развития. Практически на каждом предприятии в той или иной мере идет процесс перестройки производств», — отмечает Олег Терехов.
Например, этим летом Группа НЛМК начала масштабную экологическую модернизацию системы очистки воздуха обогатительной фабрики Стойленского ГОКа. Реализация проекта позволит в 10 раз снизить концентрацию пыли в воздухе рабочей зоны и в 2 раза валовую эмиссию пыли в атмосферу. Там же реализуется крупный проект по замене системы аспирации на дробильно-сортировочном участке обогатительной фабрики. Поэтапная замена системы очистки воздуха позволит улучшить состояние рабочих мест, в 6 раз снизить эмиссию пыли и внедрить НДТ.
В настоящее время Северсталь повышает эффективность работы и экологичность оборудования для травления металла. В результате капитального ремонта компания прогнозирует сокращение объема выбросов загрязняющих веществ в атмосферу, а также обеспечивает предельно допустимую концентрацию вредных веществ на рабочих площадках ванн травления.
Не отстают от коллег и магнитогорские металлурги. Летом ММК начал строительство доменной печи № 11. Использование передовых технологий, высокая оснащенность комплекса новой доменной печи природоохранными объектами, а также вывод из работы устаревших печей позволят ММК только в рамках этого проекта сократить выбросы вредных веществ в атмосферу на 6,6 тыс. тонн в год, а выбросов СО2 — на 1123 тыс. тонн в год. Также в электросталеплавильном цехе Магнитогорского металлургического комбината продолжается строительство пылегазоулавливающей установки для дуговой электросталеплавильной печи № 1 (ДСП-1) производительностью 2,4 млн м?/час и газоотводящих трактов электродуговых печей ДСП-1 и ДСП-2.
Экологический параметр сегодня — один из ключевых в программе модернизации устаревших производств и технологических процессов, однако не единственный.
Технологии для повышения эффективности производства
Несмотря на высокую озабоченность предприятий экологической проблематикой, ключевой задачей развития горнодобывающих и металлургических компаний является повышение эффективности производства, и данная цель непосредственно связана с выстраиванием единой взаимоувязанной цепочки управления предприятием, начиная с момента разработки продукта, его производства, заканчивая маркетингом и сбытом конечному потребителю. Данный подход закрывает еще одну глобальную цель предприятий ГМК — повышение стоимости компании в глазах инвесторов за счет обеспечения прозрачности корпоративного управления и всех бизнес-процессов. Этот фактор влияет на стоимость и оценку надежности компании наравне с финансовыми показателями, и его достижение возможно только при условии определенной степени цифровизации процессов.
В первую очередь речь идет об организации непрерывного обмена информацией, которая является основой для принятия управленческих решений, между субъектами бизнес-процессов за счет информационных технологий.
Существенным препятствием для быстрого и бесшовного выстраивания последовательной цепочки циркуляции данных является значительное количество корпоративных информационных систем (ИС), одновременно действующих на предприятиях, порой несовместимых и выдающих противоречивые данные по одному и тому же процессу.
Тем не менее задача по консолидации данных предприятия и приведению их к единому формату решается построением цифровой корпоративной платформы, которая аккумулирует сведения из разных ИС типа ERP, BPM, АСУТП, MES и пр., и является единой точкой доступа к объективной и корректной информации, равнодоступной для всех участников процесса. Таким образом, цифровая платформа становится ключевым инструментом сквозного контроля на каждом этапе цепочки производственных и бизнес-процессов и позволяет оценить их эффективность, выявить потенциальные риски, «лишние» издержки и факторы, мешающие увеличению прибыльности и пр.
Как пример, в этом году «Норникель» совместно с КРОК запустил пилотный проект по созданию озера данных для HR и производственного блоков. Это масштабируемая цифровая платформа, которая в перспективе позволит хранить и анализировать данные всей группы компаний, получая синергетический эффект при обогащении новыми данными из существующих на предприятии ИС.
Барьеры для эффективной модернизации производства
Безусловно, цифровые технологии являются инструментом для развития любого предприятия, однако реализация цифровых инициатив порой затруднена в связи с устаревшей материально-технической базой значительной части горнодобывающих и металлургических производств. Например, на старом изношенном оборудовании зачастую не установлены датчики, с помощью которых нужно получать и оцифровывать данные о состоянии агрегатов, станков и механизмов.
В процессе капитального строительства или масштабной модернизации производства у предприятий есть уникальная возможность заложить фундамент для цифрового производства, и, по мнению Олега Терехова, не стоит ее игнорировать.
Необходимо учитывать, что для эффективного внедрения цифровых технологий требуется обязательная база в виде инженерной и ИТ-инфраструктуры с высоким уровнем отказоустойчивости и безопасности. В идеале она должна проектироваться подрядчиком еще на самом раннем этапе проектирования объектов и сооружений. А значит, подрядчик должен разбираться как в производственных процессах предприятия-заказчика, так и обладать компетенциями в области ИТ и цифровых решений, которые помогут обеспечить эффективность указанных процессов. Такой подрядчик называется MAC (Main Automation Contractor) — генеральный подрядчик в части автоматизации.
Есть определенная сложность для предприятий отрасли, которые хотят работать с единым подрядчиком и отдавать проект на исполнение «под ключ». Дело в том, что в настоящее время в России отмечается дефицит MAC-подрядчиков, способных самостоятельно справиться с управлением крупными проектами по строительству или модернизации производства. Приглашенные подрядчики не обладают достаточными ресурсами и компетенциями одновременно в отраслевой, инженерно-технической и управленческой сфере для адекватной оценки потребностей проекта, самого проектного решения и организационных вопросов по его управлению.
В таких случаях заказчики вынуждены вовлекаться в процессы строительства, привлекать дополнительных исполнителей, задействовать собственные ресурсы, переключая их из других проектов. Это очень затратно с точки зрения ресурсов для заказчика, поэтому нужно выбирать генерального подрядчика, который на деле, а не на словах и на бумаге сможет стать единой точкой входа на всех этапах сопровождения проекта. Кроме того, MAC-подрядчикам обязательно нужно иметь собственные необходимые лицензии и допуски для работ на опасных производствах.
Инженерная и ИТ-инфраструктура послужит фундаментом для цифрового производства, и от того, как он будет заложен, зависит дальнейшее развитие предприятия в сторону «цифры».
Олег Терехов подчеркивает, что дальнейшая модернизация предприятий отрасли и внедрение НДТ, включая цифровые решения, выпуск современной и качественной металлургической продукции на основе экоориентированных технологий, позволят ускоренными темпами наращивать объемы производства, развивать внутреннюю инфраструктуру и реализовывать крупные инвестиционные проекты за рубежом.