Машиностроители наращивают производительность
Как участие в нацпроекте помогает уральским заводам увеличивать прибыль
Национальный проект «Производительность труда» стартовал в 2018 году. Его цель — увеличивать производительность в несырьевых отраслях экономики на 5% ежегодно, достигнув показателей Европы и США. Реализацией проекта занимается Федеральный центр компетенций в сфере производительности труда (ФЦК). А в субъектах РФ созданы Региональные центры компетенций (РЦК), которые оказывают адресную экспертную поддержку компаниям и заводам.
Успехи нацпроекта
Предприятия-участники нацпроекта ощутили экономический эффект от совместной работы с экспертами центров компетенций. В среднем выработка участников выросла в полтора-два раза, а запасы незавершенного производства (НЗП) сократились на 40%.
Большой интерес к повышению производительности труда выразили уральские предприятия.
В Свердловской области, которую признают одним из ключевых промышленных регионов страны и называют «опорным краем державы», в нацпроекте уже участвуют более ста предприятий, опережая намеченные показатели.
Опыт машиностроителей
Процесс оптимизации на предприятии длится три года и разделен на три части. Первая — диагностика выбранного участка на предприятии, вторая — внедрение улучшений путем создания потока-образца, третья — тиражирование методик и инструментов на все производственные процессы. Именно на последней, самостоятельной стадии находится АО «КМЗ» города Артёмовский, разработчик и производитель крупных тягодутьевых машин и нагнетателей. Пройдя путь совместной работы с экспертами РЦК, предприятие повысило производительность и увеличило выручку за счет внедрения принципов бережливого производства и современных систем планирования.
В качестве пилотного был выбран поток изготовления и сборки двустороннего ротора, который занимает 40% в доле выпускаемой продукции. Первая диагностика выявила 200 проблем, в том числе низкую точность производственного и оперативного планирования, потери при транспортировке и лишних передвижениях и др. Общие временные потери в потоке составляли 56 часов.
Для решения проблем было разработано 83 мероприятия: построение тянущей системы планирования, оптимизация внутрицеховой логистики, внедрение почасового производственного анализа, увеличение пропускной способности механического производства, организация рабочих мест по системе 5С и т.д.
В результате за шесть месяцев выработка на пилотном потоке выросла на 22%, незавершенное производство снизилось на треть, время протекания процесса сократилось на 66% — с 62 до 21 дня, а время выполнения заказа — более чем в два раза — со 146 до 65 дней.
Еще один опытный участник нацпроекта — Группа «СВЭЛ» — производитель электротехнического оборудования. Сразу два уральских предприятия компании вступили в нацпроект.
Так, на производстве силовых масляных трансформаторов в Екатеринбурге был оптимизирован ключевой поток. Эксперты ФЦК вместе с сотрудниками предприятия сбалансировали процессы на участках упаковки и сборки масляных трансформаторов, разработали регламенты работ операторов обмоточного оборудования пооперационных действий сборщиков, переналадили раскройную линию металла Георг.
В итоге за шесть месяцев НЗП в потоке сократилось на 22%, время протекания процессов — на треть. Это позволит Группе «СВЭЛ» дополнительно нарастить объемы производства силовых масляных трансформаторов.
Второй завод «СВЭЛ» в рамках участия в нацпроекте оптимизировал поток производства сухих трансформаторов. Для этого был создан виртуальный склад хранения обмоток, оптимизированы производственные запасы, организованы тянущие системы с внешними поставщиками и др. Компания повысила выработку в пилотном потоке на четверть, а время изготовления одного трансформатора сократилось на 42%. Участие в нацпроекте позволило производству сухих трансформаторов получить дополнительную прибыль и увеличить выпуск продукции.
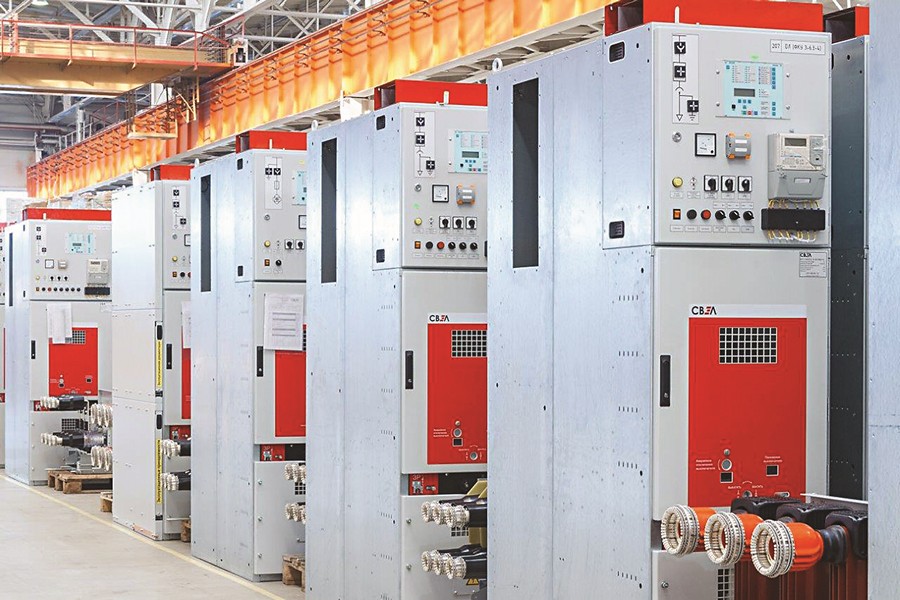
Также шестимесячную работу эксперты ФЦК провели на екатеринбургском ЗАО «Завод ЭМА». Один из крупнейших заводов электромедицинской аппаратуры в стране оптимизировал поток изготовления хирургических светильников «Эмалед» — своего ключевого продукта.
На момент старта проекта оборудование было расставлено таким образом, что приходилось перемещаться по этажам, тем самым увеличивая время и затраты на производство. Оптимизация и перепланировка участков производственных цехов позволили сократить перемещение на 260 метров и высвободить пространство под новое производство. Создание системы прослеживаемости сырья и материалов в режиме реального времени позволило блокировать брак до входа в производство, что сократило время протекания процесса на восемь часов. В итоге выработка на заводе выросла на 62%, а переход к позаказному производству позволил снизить НЗП на 30%.
Как стать участником нацпроекта
До 2024 года присоединиться к проекту могут предприятия с выручкой от 400 млн рублей, занятые в одной из пяти сфер — обрабатывающей промышленности, строительстве, транспорте, сельском хозяйстве и торговле. На предприятиях со средней выручкой от 2 млрд рублей активная фаза работы специалистов центров компетенций может составить 12 месяцев.
Программа улучшений на предприятиях рассчитана на три года:
• Регистрация (до пяти рабочих дней). Для вхождения в нацпроект нужно подать заявку на портале производительность.рф.
• Активная фаза (от 6 до 12 месяцев в зависимости от размеров предприятия). В это время на площадке работают эксперты центров компетенций.
• Фаза самостоятельной работы (2,5 года). Предприятие самостоятельно тиражирует улучшения на другие потоки производства.