Особенности прогнозирования поломок и внеплановых остановов оборудования на предприятиях нефтегазохимической отрасли в России
Регулярно на предприятиях нефтегазохимической отрасли возникают инциденты, связанные с неисправностями технологического оборудования. Зачастую происходят остановы производственного процесса, и предприятие несет колоссальные финансовые убытки. Внеплановый останов добычи одной скважины — это сотни тонн и кубометров недополученного сырья, останов оборудования НПЗ ведет к нарушениям во всей цепочке поставок, не говоря о потерях сырья и товарных продуктов.
Количество инцидентов можно сократить за счет корректного прогнозирования потенциальных поломок и неисправностей оборудования. Глубокий анализ данных с их последующей интерпретацией дает инженерам возможность предсказывать потенциальную неисправность оборудования, оптимизировать расписание диагностических проверок, сокращая количество избыточных ремонтов, а также улучшать эффективность использования техники и увеличивать срок службы оборудования за счет превентивного выявления возможных поломок.
В России прогнозная аналитика на производствах только набирает обороты, ее внедрение на отечественных нефтегазовых и нефтехимических предприятиях идет постепенно, однако в мировой практике ТОиР зарубежные промышленные предприятия уже давно используют прогнозную модель обслуживания оборудования и применяют аналитику на основе больших данных.
British Petroleum сократил сроки строительства скважин на 30%, а общую стоимость скважин — на 15%.
Благодаря системам прогнозирования и упреждения осложнений при эксплуатации скважин установками электроцентробежных насосов на морских платформах, компании British Petroleum удалось снизить эксплуатационные затраты более чем на 2 млн долларов за счет повышения межремонтного периода работы скважин и уменьшения времени простоя в ожидании ремонта.
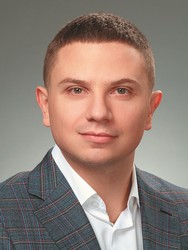
О том, как технологии прогнозной аналитики помогают собирать и анализировать массивы данных для получения специалистами исчерпывающей картины о состоянии оборудования и предсказания неисправностей и отказов, рассказал директор по развитию бизнеса ИТ-компании КРОК в нефтегазовой и химической промышленности Игорь Зельдец.
Аналитика Big Data для прогнозирования неисправностей разного типа оборудования
Ответственность за поддержание оборудования в исправном состоянии на нефтегазовых и химических предприятиях закреплена за службами Главного инженера. Сотрудники данных служб контролируют состояние техники, прогнозируя возможные отказы путем анализа данных, поступающих с КИПиА, IoT-устройств, и принимают меры, направленные на снижение риска возникновения поломок и незапланированных остановов оборудования. Основой для эффективного прогнозирования является поток данных, поступающих с нефтегазовых объектов, и его объемы растут с каждым днем. К примеру, обычная буровая вышка создает около 1 ТБ данных в день. Один-единственный датчик, раз в секунду фиксирующий тот или иной параметр (например, температуру), за год производит более 31,5 млн значений. А на современном нефтеперерабатывающем или химическом заводе таких датчиков могут быть десятки тысяч. Для того чтобы справляться со сбором и управлением таким массивом данных, в 2020 году уже свыше четверти (28,5%) российских промышленных компаний использовали Big Data в бизнес-процессах (согласно исследованиям ИСИЭЗ НИУ ВШЭ).
Big Data позволяет консолидировать, хранить, анализировать информацию о состоянии оборудования на основе данных, полученных из различных источников. В роли источников информации могут выступать как структурированные (табличные) данные, так неструктурированные (фото, видео) и полуструктурированные (различные данные телеметрии, логи событий, геоданные и др.).
На основании данных, поступающих с оборудования КИПиА, IoT-датчиков и других источников, инженер эксплуатационной службы:
• анализирует техническое состояние оборудования на основе информации о дефектах и отказах по результатам диагностирования оборудования;
• оценивает риски выхода оборудования из строя;
• анализирует соблюдение правил эксплуатации оборудования;
• анализирует технологические карты, стандартные операционные процедуры (СОП) на достаточность/избыточность ремонтных мероприятий, направленных на снижение риска отказа оборудования;
• оценивает уровень надежности и критичности оборудования;
• проводит RCM, RBI, FMEA, FMECA анализ;
• проводит анализ коренных причин отказов оборудования (RCA);
• определяет виды дефектов и износов оборудования (усталостный, тепловой, гидро-абразивный, адгезивный, внешний и функциональный, совокупный, окислительный, коррозийный, кавитационная эрозия, брак, водородное охрупчивание, и т.д.).
В СИБУР была разработана комплексная система прогнозной аналитики
Система прогнозной аналитики Сибура в режиме реального времени следит за показателями экструзии и полимеризации с помощью видеонаблюдения и IIoT-датчиков. На основании этих данных система прогнозирует аварийный останов из-за наличия агломератов в экструзионной смеси. В этом случае операторы АСУТП получают предупреждение и могут предотвратить аварию, усилив прижим ножей или изменив настройки экструдера. Данная технология успешно эксплуатируется на предприятии с 2018 года, обеспечив полное отсутствие незапланированных остановов. Для сравнения, в 2017 году на предприятии было зафиксировано 19 прецедентов с аварийным остановом оборудования.
Барьеры для внедрения прогнозной аналитики на основе Big Data на нефтегазовых и химических производствах
Благодаря широким возможностям технологии Big Data, тренд на ее использование будет только нарастать. Количество датчиков на промышленных предприятиях ежегодно растет в геометрической прогрессии. К концу 2019 года в мире насчитывалось 7,6 млрд устройств, подключенных к промышленному интернету, а к 2030 году количество этих приборов увеличится до 24,1 млрд.
Несмотря на преимущества, которые дает технология Big Data, остаются определенные барьеры для широкого использования прогнозной аналитики в части управления техническим состоянием оборудования на промышленных предприятиях.
В первую очередь речь идет о качестве и достоверности собираемых данных, точности и корректности алгоритмов интерпретации полученных сведений. До сих пор на предприятиях прогнозная аналитика воспринимается как «черный ящик», через который пропускают данные. В результате, несмотря на то, что использование технологии больших данных уже официально закреплено в ряде должностных инструкций отделов диагностики и мониторинга оборудования нефтегазохимических компаний, инженеры по надежности не доверяют результатам «из ящика» и предпочитают работать вручную.
Каким же образом можно преодолеть факторы, связанные с достоверностью, полнотой данных и недоверием сотрудников к результатам на выходе?
Достоверность и полнота больших данных
Говоря о прогнозной аналитике, необходимо отметить важность полноты и достоверности получаемой инженерами информации, на базе которой эта аналитика формируется. Ее консолидация ведется из разных источников — часть данных поступает со всевозможных датчиков (температурные, вибрационные, контроля давления и пр.), другая часть — из многочисленных корпоративных систем управления (ИСУ ТОиР, ERP, Системы диагностики, ТО и мониторинга оборудования и пр.) и других ресурсов (MES, локальные осмотры объектов и др.). В каждой системе управления часто применяются различные форматы записей, что может привести к искажению или дублированию информации. Кроме того, для предприятий нефтегазохимической промышленности характерна территориально-распределенная структура, когда мониторинг определенных объектов ведется удаленно и вручную.
Данная проблема решается созданием на предприятии единой информационной среды (цифровой платформы), позволяющей стандартизировать и консолидировать данные из различных источников. Цифровая платформа является единой точкой доступа к получению корректной информации, исключает вероятность построения матмоделей и прогнозной аналитики на базе недостоверных данных.
Наличие единого доступа к данным позволяет ускорить процессы поиска информации инженерами по всем информационным системам предприятия без вовлечения сотрудников других структур. Кроме того, консолидация информации из разных систем способствует обогащению объектов дополнительными параметрами и показателями.
Объективность больших данных
У пользователей — инженеров служб эксплуатации — возникает справедливый вопрос: «По каким алгоритмам и на основании каких математических формул строится прогнозная аналитика?». «Почему этот показатель оказался в “красной” зоне?». Технология прогнозной аналитики задействует множество методов статистики, интеллектуального анализа данных, учитывает, как текущие показатели в режиме реального времени, так и исторические данные, различные паттерны и другие наборы условий. Не имея достаточного понимания о том, как именно формируются результаты прогнозной аналитики и насколько корректны применяемые матмодели и алгоритмы в ней, у инженера нет доверия к полученным аналитическим отчетам.
Для решения данной проблемы внедряемые алгоритмы и модели прогнозной аналитики должны быть основаны на связке производственных данных с бизнес-процессами и с учетом специфики функционирования конкретного объекта. Только при такой синхронизации, по мнению Игоря Зельдеца, возможно получить желаемый бизнес-эффект.
Специалисты промышленных отраслей постепенно внедряют прогнозную аналитику и Big Data и оценивают, насколько их применение может быть экономически оправданным на производстве, ведь внедрение таких систем всегда требует значительных временных и финансовых затрат. Тем не менее ежегодно растет количество успешных кейсов по внедрению прогнозной аналитики с подтвержденным бизнес-эффектом, и крупные игроки рынка считают, что в перспективе данный инструмент станет неотъемлемой частью технологических процессов, особенно там, где речь идет о крупном непрерывном производстве.